Scroll down for more
Striking a Balance: Managing Stockouts and Overstocking in E-commerce
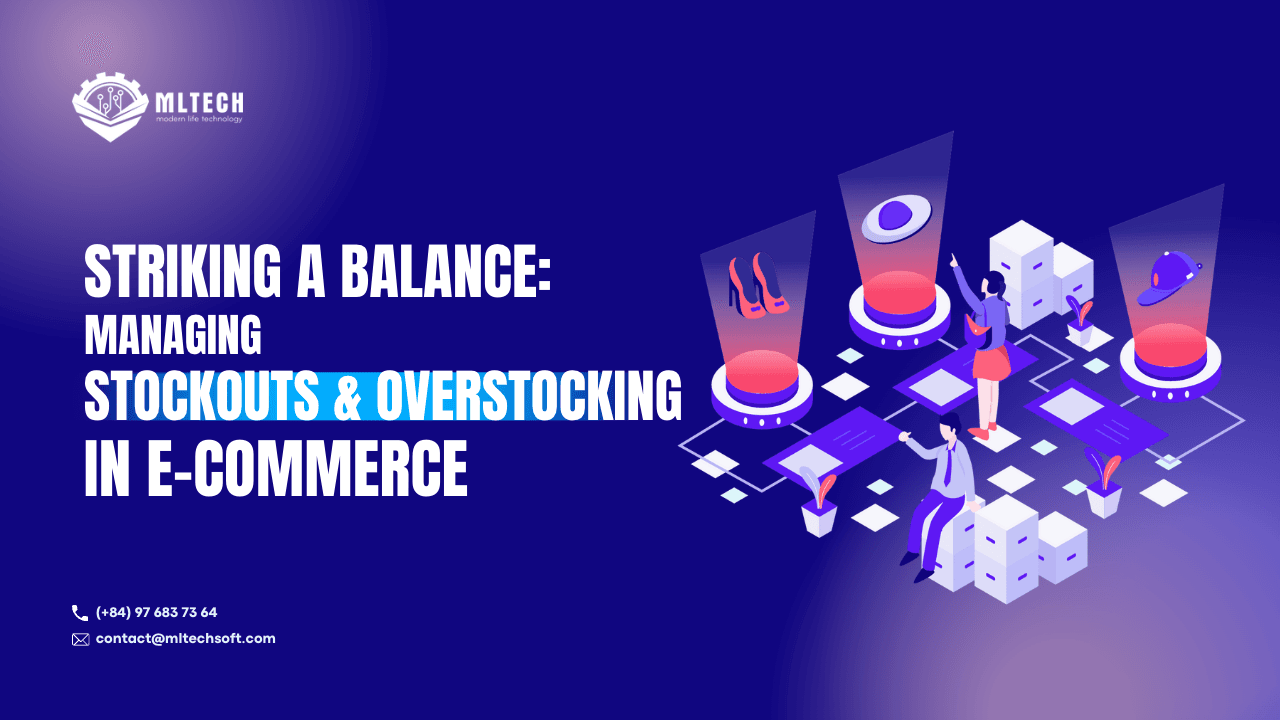
Aside from understocking and overstocking, poor inventory management results in inefficiencies due to the lack of accurate, real-time information about inventory volumes. This increases the risk of errors when reordering inventory from suppliers or selling unavailable inventory.
The negative impact of stockouts and overstocking on e-commerce businesses
Inventory levels affect customer satisfaction. Customers are more likely to purchase the product (or a similar product) from a competitor, thus eroding customer loyalty, tarnishing the image of the brand, and creating a feeling of unprofessionalism and untrustworthiness.
The benefits of managing inventory levels effectively
Improved accuracy: Real-time inventory tracking helps improve inventory management and ensure optimal inventory to fulfill orders
Reduce costs: Improving the efficiency of inventory management eliminates sources of error, and fewer errors ultimately mean fewer resources to spend troubleshooting.
Save time: Automate your inventory management process, save time on inventory forecasting, and streamline your pickup process with robotics and AI.
Improved business plan: An internal inventory management strategy gives you the business insight you need to scale your business and continuously improve your operations.
Improve customer service: Providing your customers with a great shopping experience is essential to survival in today's competitive e-commerce space. Satisfied customers not only increase the likelihood of repeat purchases, but good reviews and word of mouth also help you get more conversions.
Strategies for Managing Inventory Levels Effectively:
Inventory management is a key factor in a company's profitability, but many small businesses do not have adequate control over the products they sell. Some companies are short on inventory and unable to meet customer expectations with a sufficient supply of available products. This often leads customers to move to another store or leave forever.
Inventory management software
An inventory management system is a combination of hardware and software technologies that track and manage product inventory, product sales, and other manufacturing processes.
Analyze sales trends and forecast demand
Trend forecasting is the process of using market research and consumer data to predict future customer buying habits and preferences. Trend forecasting provides product designers with insights to help them design items that their target audience will love and buy.
Conduct regular inventory audits
An inventory audit compares a company's financial and inventory records to ensure that they match its physical inventory counts. Ensuring inventory accuracy and identifying discrepancies in inventory counts and financial records is a critical process.
Adopt a just-in-time inventory management strategy
A just-in-time (JIT) inventory system is a management strategy that allows companies to receive goods as close as possible to the time they actually need them. So when an automobile assembly plant needs to install airbags, they receive the airbags when the automobile arrives at the assembly line rather than storing them on a shelf.
Maintain safety stock levels
The optimal level depends on several factors, including inventory velocity, current and future demand, sales volume, and supplier lead times. As a rule of thumb, safety stock should be the amount of inventory consumed per day multiplied by the lead time (days).
Tools and Technologies for Effective Inventory Management
- Collecting barcode data.
- A perpetual inventory system relies heavily on timely and accurate reporting.
- Cycle count for improved accuracy.
- ABC analysis for prioritization.
- Integrated planning and execution.
- Batch tracking and traceability.
Overview of different tools and technologies that can help businesses manage their inventory levels effectively
Here are the top technologies:
- Warehouse management software.
- Barcode system.
- RFID tag.
- Internet of things
- LiFi technology. artificial intelligence.
- Machine learning.
- Automated picking tool.
RFID technology
RFID (Radio Frequency Identification) is a form of wireless communication that uses electromagnetic or capacitive coupling in the high-frequency portion of the electromagnetic spectrum to uniquely identify an object, animal, or person.
How does RFID work?
All RFID systems consist of three components: Scanning antennas, transceivers, and transponders. A scanning antenna combined with a transceiver is called an RFID reader or interrogator.
There are two types of RFID readers: fixed readers and portable readers. RFID readers are network-connected devices that can be portable or permanently attached. It uses radio waves to send a signal that activates the tag. Once activated, the tags send waves back to the antenna, where they are converted into data.
Barcode scanners
A barcode reader, also known as a price scanner or point-of-sale (POS) scanner, is a portable or stationary input device used to capture and read the information contained in barcodes.
An example of a barcode reader is a supermarket barcode scanner that reads and records the price of an item. The image is an example of an HP barcode reader. Many smartphones now, with the right app, can also scan and read barcodes.
Warehouse management systems
There are four types of WMS systems for 3PL companies. These are standalone warehouse management systems, supply chain execution modules, integrated ERP (enterprise resource planning), and cloud-based systems.
All major WMS vendors (IBM, Microsoft, Oracle, and SAP) offer various deployment options, including cloud-based systems. WMS providers that are primarily cloud-based or cloud-only include Fishbowl, HighJump, and SnapFulfil.
Order management systems
Customer relationship management (CRM) is a software program that manages customer information, such as contact information and past transactions.
Order Management System (OMS) meanwhile tracks orders and automates order management operations. An OMS is a computer software system that automates the tracking of sales, orders, inventory, and fulfillment. Some of these solutions also help brands monitor people, processes, and partnerships.
Conclusion
Overstock and understock are common problems around the world, regardless of business type, size, or location. Both are two sides of the same coin. If you want to avoid overstocking, the risk of facing stock shortages increases.
On the other hand, if you want to avoid stock shortages, the risk of facing overstock increases. A safe line should be maintained where both risks are mitigated. Advanced inventory tools help measure safety lines for specific products based on needs analysis.
Get our blog
Want the latest and greatest from our blog straight to your inbox? Chunk us your details and get a sweet weekly email.
Read more in our blog
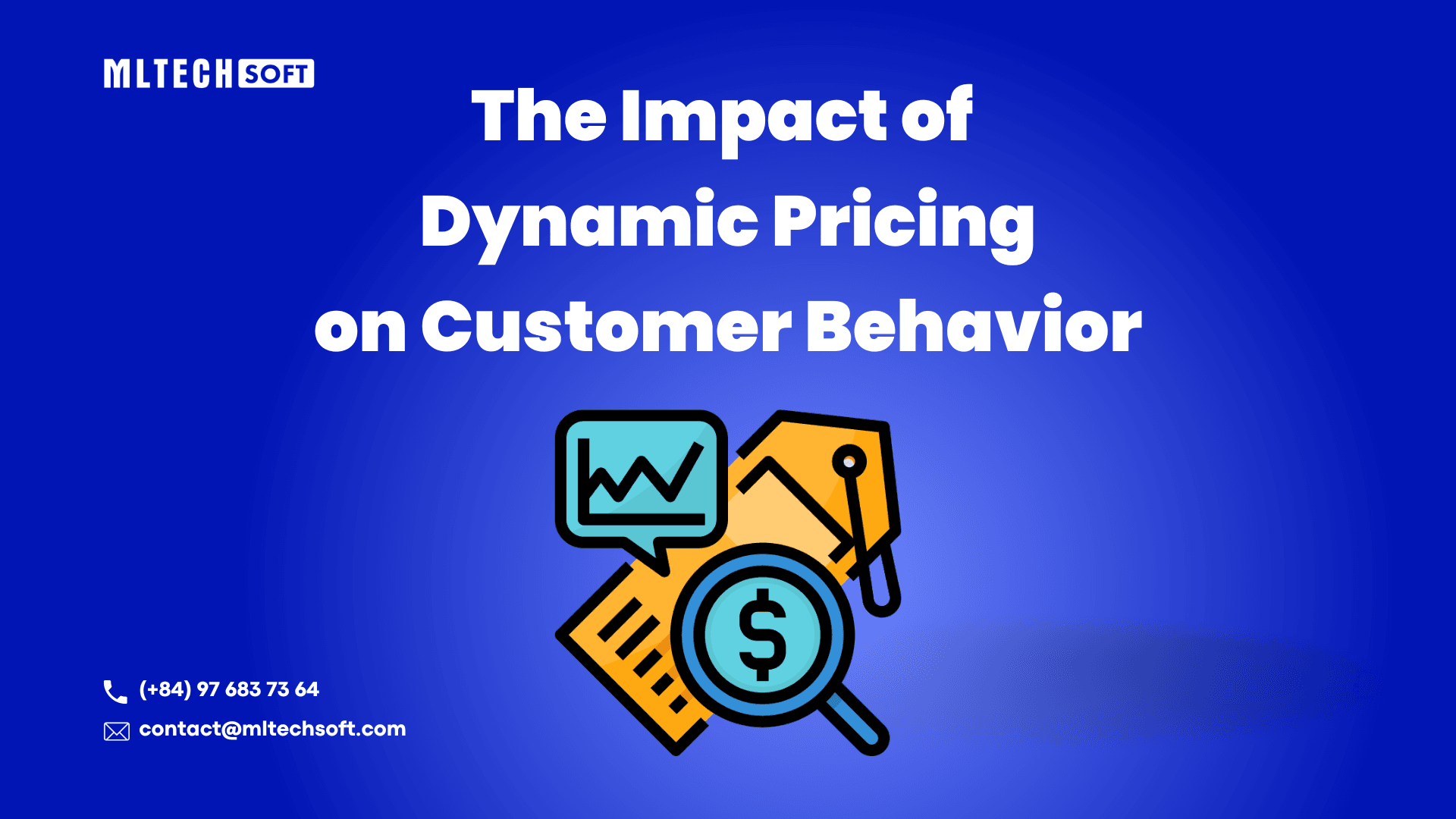
Project Management
The Impact of Dynamic Pricing on Customer BehaviorExplore the impact of dynamic pricing on customer behavior and learn how to implement effective pricing strategies.
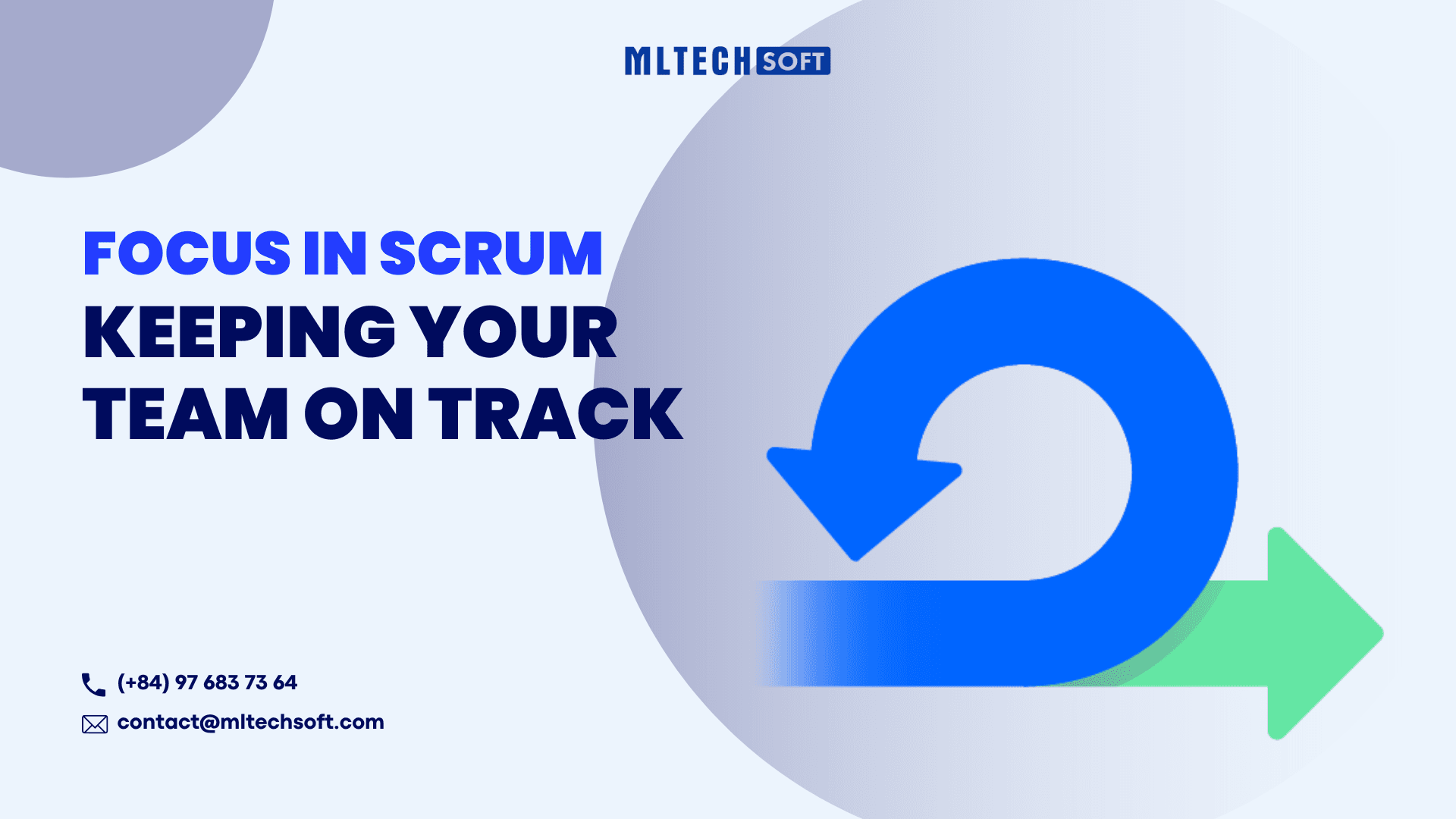
Project Management
Focus in Scrum: Keeping Your Team on TrackDiscover effective strategies to maintain focus within your Scrum team, overcome common challenges, and boost productivity.
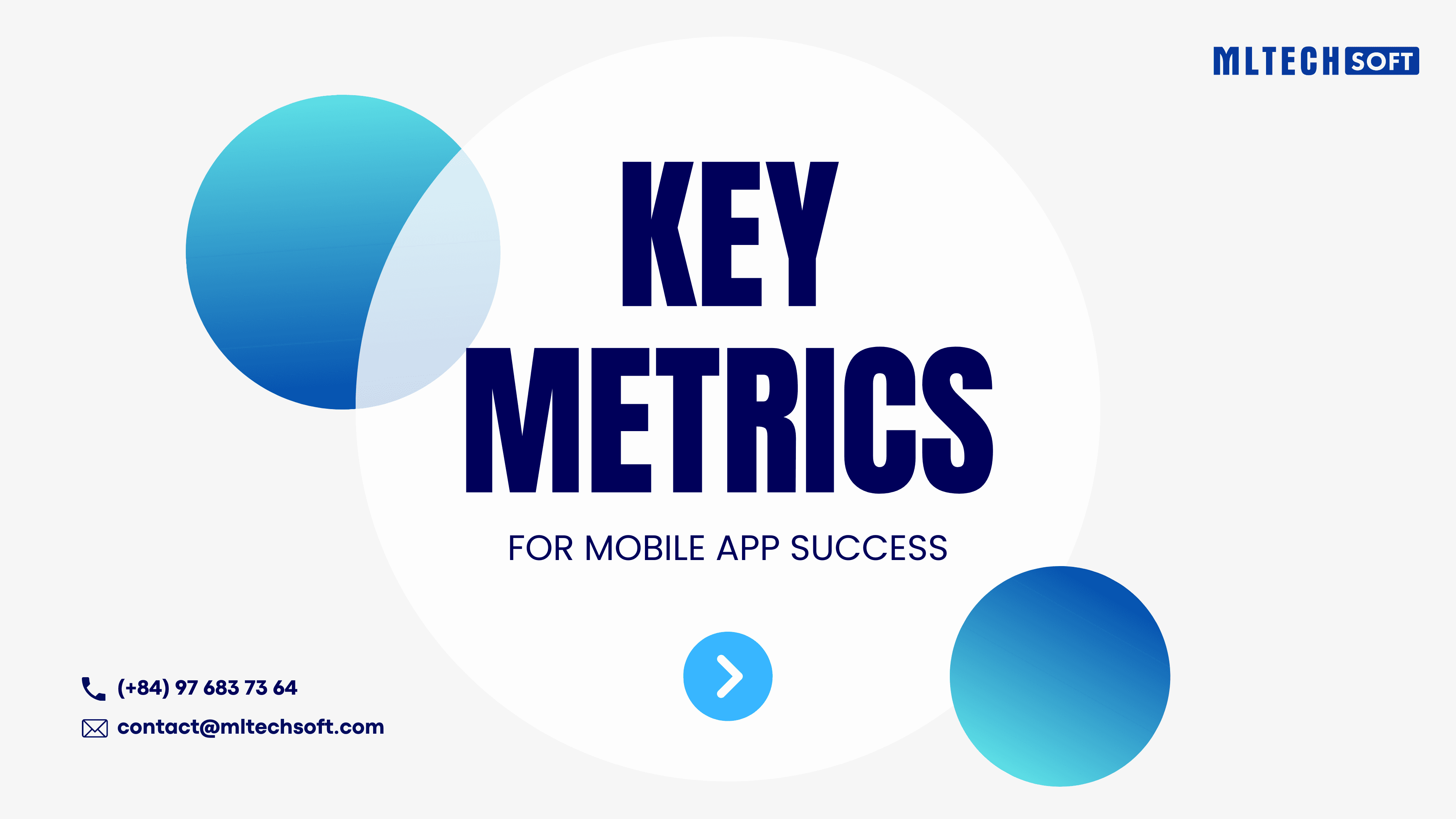
Project Management
Key Metrics for Mobile App SuccessDiscover the essential metrics for mobile app success, from user acquisition and engagement to monetization and performance.
MLTECH SOFT