Scroll down for more
Inventory Control Methods: FIFO, LIFO, and ABC Analysis Explained
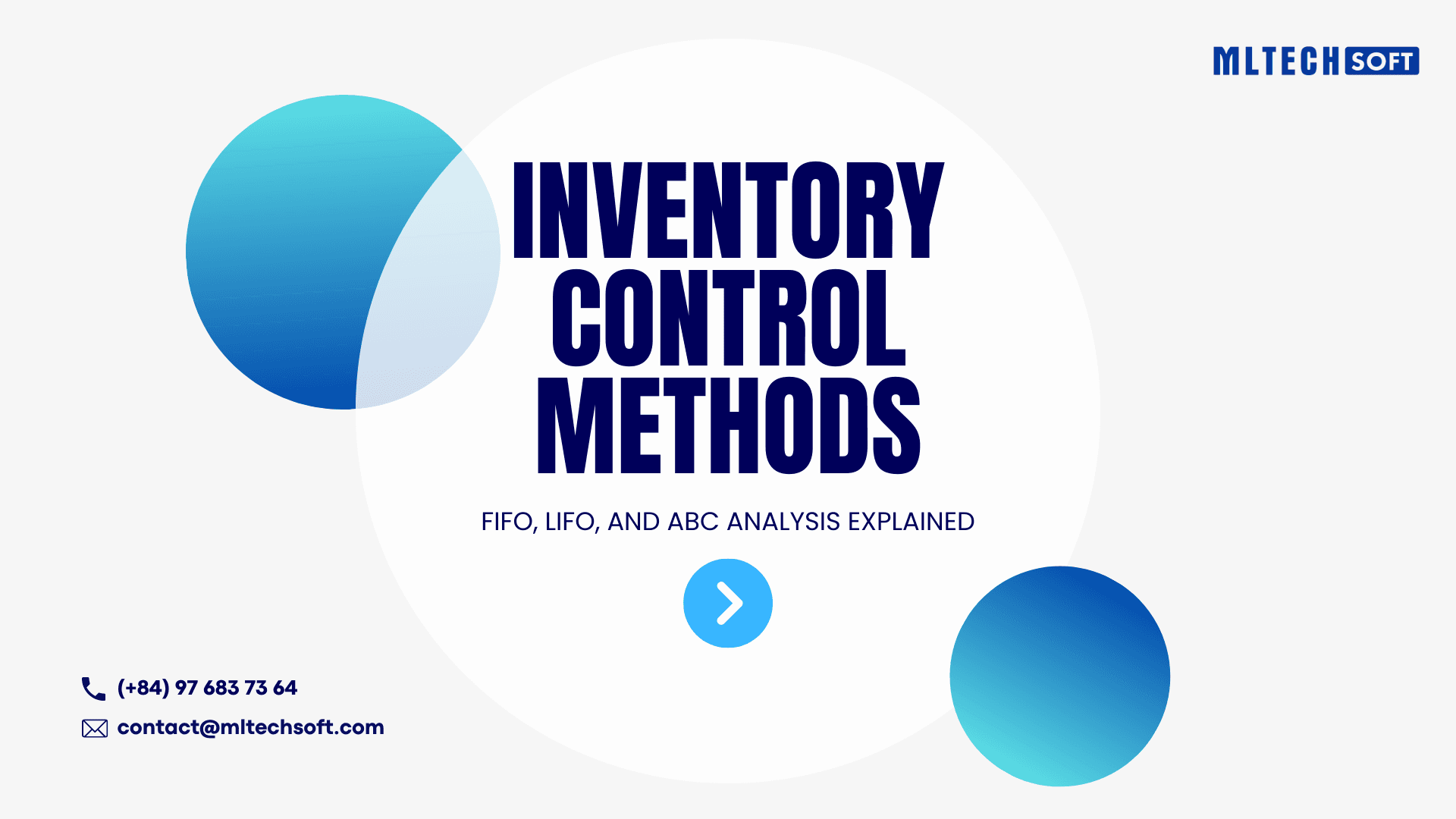
There is no handbook for supporting employees during a pandemic. The best we can do is provide a strong set of resources, learn from experience, and seek feedback from our employees. Consider implementing regular polls, check-ins, or polls to understand the impact and success of your offering. Make sure the benefits you offer have clear success metrics.
1. A brief overview of inventory control in supply chain management
The most important and difficult role inventory plays in the supply chain is to facilitate the balance between supply and demand. To effectively manage supply chain flows, companies must address upstream supplier exchanges and downstream customer requirements. This allows companies to strike an important balance between meeting customer demand, which is often difficult to accurately predict, and maintaining an adequate supply of materials and goods.
2. Introduction to the three inventory control methods: FIFO, LIFO, and ABC Analysis
FIFO - FIRST IN, FIRST OUT - means that the goods put in first are taken out first. Products returned to salable inventory must be arranged so that the first-in, first-out system works effectively.
LIFO - LAST IN, FIRST OUT - means that the goods stored last are the first to be retrieved. Carefully and systematically load vehicles and containers using the LIFO principle to save time during unloading, prevent property damage, and reduce safety risks. Special care must be taken when loading and unloading boxes to avoid damage.
ABC ANALYSIS is an inventory classification technique that divides commodities into three revenue-based categories. In ABC analysis, 'A' represents the most significant items, 'B' represents moderately necessary commodities, and 'C' represents the least important inventories.
3. FIFO (First-In, First-Out)
3.1. Definition and explanation of the FIFO method
First In, First Out (FIFO) is an inventory method that assumes the first goods purchased are the first goods sold. This means that older inventory will get shipped out before newer inventory, and the prices or values of each piece of inventory represent the most accurate estimation.
For example, if a batch of 1,000 items is manufactured in the first week of the month and another batch of 1,000 items is manufactured in the second week, the first batch manufactured will sell first. The logic behind the FIFO method is to prevent inventory obsolescence.
3.2. Benefits and advantages of using FIFO in inventory management:
FIFOs typically increase inventories on the balance sheet during periods of inflation. As the cost of goods sold usually goes down, so does the net profit. While this may be considered better, it can also result in a higher tax liability.
Easy to understand, widely accepted, and trusted. FIFO follows the natural flow of inventory (the oldest product is sold first, and its cost is calculated first). This simplifies bookkeeping and reduces the chance of errors.
More storage space. Products can be packed more compactly, freeing up additional floor space in the warehouse. Warehouse operations are streamlined.
Minimize inventory turnover. Possible strategies include reducing backorder quantities and safety stock, and using marketing campaigns and pricing strategies to increase demand and sell inventory faster before customers completely lose interest.
Improved quality control: Better quality control can increase profits. It also improves employee and customer satisfaction. Organizations seeking a proactive approach to employee, customer, and manager health can do so through improved quality management.
Warranty management: Manufacturers use warranty management software to handle all accounting and process management related to warranties for their products. This includes requests for inspections, complaints, returns, registrations, etc.
Whether it's waiting for a bus, waiting in front of an elevator or vending machine, or lining up for the toilet, the person in front of you goes before the person behind you.
Gross profit tends to be overstated, especially during periods of high inflation, leading to misleading financial reporting. Costs appear lower than they really are, and profits appear higher than they actually are.
4. LIFO (Last-In, First-Out)
4.1. Definition and explanation of the LIFO method:
Last In, First Out (LIFO) is a method of calculating inventory levels. In LIFO, the cost of recently purchased (or manufactured) products is expensed first. Generally Accepted Accounting Principles (GAAP) apply to LIFO only in the United States.
4.2. Benefits and advantages of using LIFO in inventory management:
Most companies that choose to use LIFO over FIFO do so for tax benefits. However, there may be tax obligations. Since the only real purpose of adopting LIFO is to avoid paying high taxes, the advantage of LIFO is also a disadvantage, which generally means lower profits.
4.3. Practical examples and scenarios where LIFO is applicable
Inflationary environments: LIFO is often employed during periods of inflation when prices are rising. By assuming that the most recently acquired inventory is sold first, LIFO matches higher-priced inventory with current revenue. This approach helps reduce taxable income and manage cash flow by recognizing higher costs of goods sold (COGS) and lower profits.
Industries with rapidly changing costs: LIFO is suitable for industries where the costs of raw materials or goods can fluctuate significantly over short periods. For example, the oil and gas industry experiences frequent price fluctuations, and LIFO allows companies to account for the most recent purchases at the higher market prices, providing a more accurate reflection of the cost of goods sold.
Perishable goods: LIFO is often used in industries dealing with perishable goods, such as food and agriculture. Perishable items have limited shelf lives, and using LIFO ensures that the most recently acquired inventory is sold first, reducing the risk of spoilage or obsolescence.
Retail and consumer goods: LIFO can be applicable in the retail industry, particularly for businesses that deal with products that have a short lifecycle or are subject to frequent style changes or technological advancements. For example, in the fashion industry, where trends change rapidly, using LIFO allows retailers to account for the cost of the latest inventory sold.
Businesses with decreasing inventory costs: LIFO may be suitable for businesses that experience a consistent decline in the cost of their inventory over time. By assuming that the most recent purchases are sold first, LIFO can lead to lower COGS and potentially higher reported profits.
Tax planning and reduction: LIFO can be used as a tax planning strategy to reduce tax liabilities. By matching higher costs with current revenues, LIFO can lower taxable income during inflationary periods, resulting in reduced tax obligations.
FIFO method not reflective of actual flow: In some cases, businesses may find that the FIFO (First-In, First-Out) method does not accurately reflect the actual flow of inventory. This may occur if the business has a specific order fulfillment process or handles inventory in a non-chronological manner. In such scenarios, LIFO can provide a more accurate representation of inventory management practices.
4.4. Key considerations and challenges when implementing LIFO
IFRS (International Financial Reporting Standards) is a not-for-profit responsible for developing global accounting and sustainability disclosure standards, known as IFRS Standards. IFRS prohibits LIFO because it can distort a company's profitability and financial statements. For example, LIFO may understate a company's earnings in order to keep taxable income low. It's also possible that your inventory valuation is out of date.
4.5. Tips for effective implementation of LIFO in supply chains
Last in, first out (LIFO) is an inventory management and valuation method in which the last inventory produced or purchased is the first to be sold, used, or disposed of.
5. ABC Analysis Method
5.1. Definition and explanation of the ABC analysis method
ABC analysis is an inventory management technique that determines the value of inventory items based on their importance to the business. ABC classifies items based on need, cost, and risk data. Inventory managers group items into classes based on these criteria.
5.2. Benefits and advantages of using ABC analysis in inventory management
ABC analysis is a valuable tool in inventory management that classifies items based on their value and importance. It provides numerous benefits and advantages, particularly for large manufacturing companies. Here are the key advantages of using ABC analysis:
Efficient resource allocation: ABC analysis helps companies allocate their resources effectively by identifying the most critical inventory items. It categorizes items into three groups: A, B, and C, based on their value or contribution to overall sales or profitability. By focusing on high-value items (A-items) and allocating more resources to them, companies can ensure efficient utilization of their resources.
Increased inventory turnover: Implementing ABC analysis enables companies to prioritize their inventory management efforts. This focus on high-value items to improve inventory turnover rates, as companies ensure that these items are well-stocked, readily available, and not tied up in excess inventory.
Optimal stock control: ABC analysis allows for a more precise and tailored approach to inventory control. For example, A-items might require frequent replenishment and tighter inventory control, while C-items can be managed with more relaxed policies. This leads to better stock control, reduced stockouts, and minimized carrying costs.
Cost reduction: ABC analysis helps in cost reduction by identifying items that are responsible for the majority of inventory costs. A-items, being high-value and high-impact, often have higher carrying costs associated with them. By focusing on managing these items more effectively, such as through implementing just-in-time (JIT) inventory practices or negotiating better pricing with suppliers, companies can reduce carrying costs and overall inventory holding costs.
Time savings: With ABC analysis, companies can prioritize their efforts and streamline their inventory management processes. By focusing on the critical A-items, companies can save time by allocating resources, attention, and decision-making efforts to the most valuable products.
Improved customer service: By effectively managing high-value items (A-items), companies can ensure better customer service. These items typically have higher demand and greater customer importance.
5.3. Practical examples and scenarios where ABC analysis is applicable
ABC analysis typically divides inventory into three categories based on revenue and required management actions.
Items account for 20% to 80% of sales, so 'A' is required. 'B' consists of 30% products and 15% sales. On the other hand, 'C' means 50% with at least 5% turnover and is therefore treated as the most liberal.
While the numbers for specific companies may vary, they share similar, identifiable patterns. The purpose of this analysis is to draw management's attention to a few important items (A items) rather than a large number of insignificant items (C items) and direct inventory management efforts to the individual items with the most inventory. It's about concentrating for maximum effect.
5.4. Key considerations and challenges when implementing ABC analysis
ABC is not a simple or easy method to implement. It requires extensive data collection, analysis, and interpretation. It also requires a significant investment of time, money, and resources. Deploying ABC can face technical, behavioral, and organizational challenges.
6. Comparison and Selection of Inventory Control Methods
6.1. Factors to consider when selecting the appropriate method for specific businesses
It's important to plan your budget in advance so that you can adequately fund your business idea.
New small business owners may feel relaxed about their business and not feel the need to stick to budgets. However, if you want to plan for the future of your business, you need to invest in planning. Budgeting is the most effective way to manage cash flow and allows you to invest in new opportunities at the right time.
As your business grows, you may not always be able to practice all parts of it. You may need to divide your budget into different areas, such as sales, production, and marketing. You can see that money flows in different directions within an organization. A budget is an important tool for ensuring that your spending is under control.
Nature of the business: The industry and type of business play a crucial role in selecting the method. Consider whether the business deals with perishable goods, time-sensitive products, or goods with a short shelf life. Some methods, like FIFO, are more suitable for industries with perishable goods, while others, like LIFO, may be better for industries with rising prices.
Market conditions: Evaluate the prevailing market conditions, such as inflation or deflation. LIFO may be advantageous during inflationary periods, while FIFO may be more appropriate during deflationary periods. Consider how each method aligns with the pricing trends in the industry.
Cost flow and valuation objectives: Determine the desired cost flow and inventory valuation objectives of the business. FIFO provides a better reflection of current market prices, while LIFO may result in a cost advantage during inflation. Consider the impact on financial statements, tax liabilities, and the business's specific reporting requirements.
Tax implications: Evaluate the tax regulations and implications associated with each method. LIFO may lead to lower taxable income during inflationary periods, while FIFO may result in higher taxable income. Consult with tax professionals to understand the tax consequences and how they align with the business's tax strategy.
Financial reporting requirements: Consider the financial reporting standards and requirements applicable to the business. Some jurisdictions or reporting frameworks may have specific rules regarding inventory valuation methods. Ensure that the chosen method complies with the relevant reporting guidelines.
Inventory characteristics: Analyze the characteristics of the inventory, such as turnover rate, obsolescence risk, and carrying costs. FIFO can be advantageous for high turnover items or goods prone to obsolescence, while LIFO may be suitable for slower-moving inventory.
Cost accounting considerations: If cost accounting is a significant concern, evaluate how each method aligns with the business's cost accounting system. ABC Analysis, while not directly determining cost flow or valuation, can provide valuable insights for resource allocation and inventory management based on value or importance.
Management objectives: Consider the specific goals and objectives of the business. Determine whether the primary focus is on maximizing profitability, reducing tax liabilities, optimizing inventory control, or improving financial reporting accuracy. The chosen method should align with these objectives.
IT systems and capabilities: Assess the business's information technology (IT) systems and capabilities. Some methods may require sophisticated inventory tracking systems or software integration. Ensure that the chosen method can be effectively implemented within the existing IT infrastructure.
Operational impact: Evaluate the operational implications of each method. Consider the impact on order fulfillment, stock control, and inventory management processes. The selected method should align with the business's operational efficiency and customer service objectives.
Conclusion
Companies can choose from a number of different accounting methods for taking inventories, but there are restrictions associated with IFRS. Two of these options are LIFO and FIFO. Companies that choose the LIFO method typically sell up-to-date inventory that is expensive to source or produce. On the other hand, the FIFO method results in lower selling costs and higher inventory levels. A company's taxable income, net profit, and balance sheet balance depend on the inventory method chosen.
Content
Get our blog
Want the latest and greatest from our blog straight to your inbox? Chunk us your details and get a sweet weekly email.
Read more in our blog
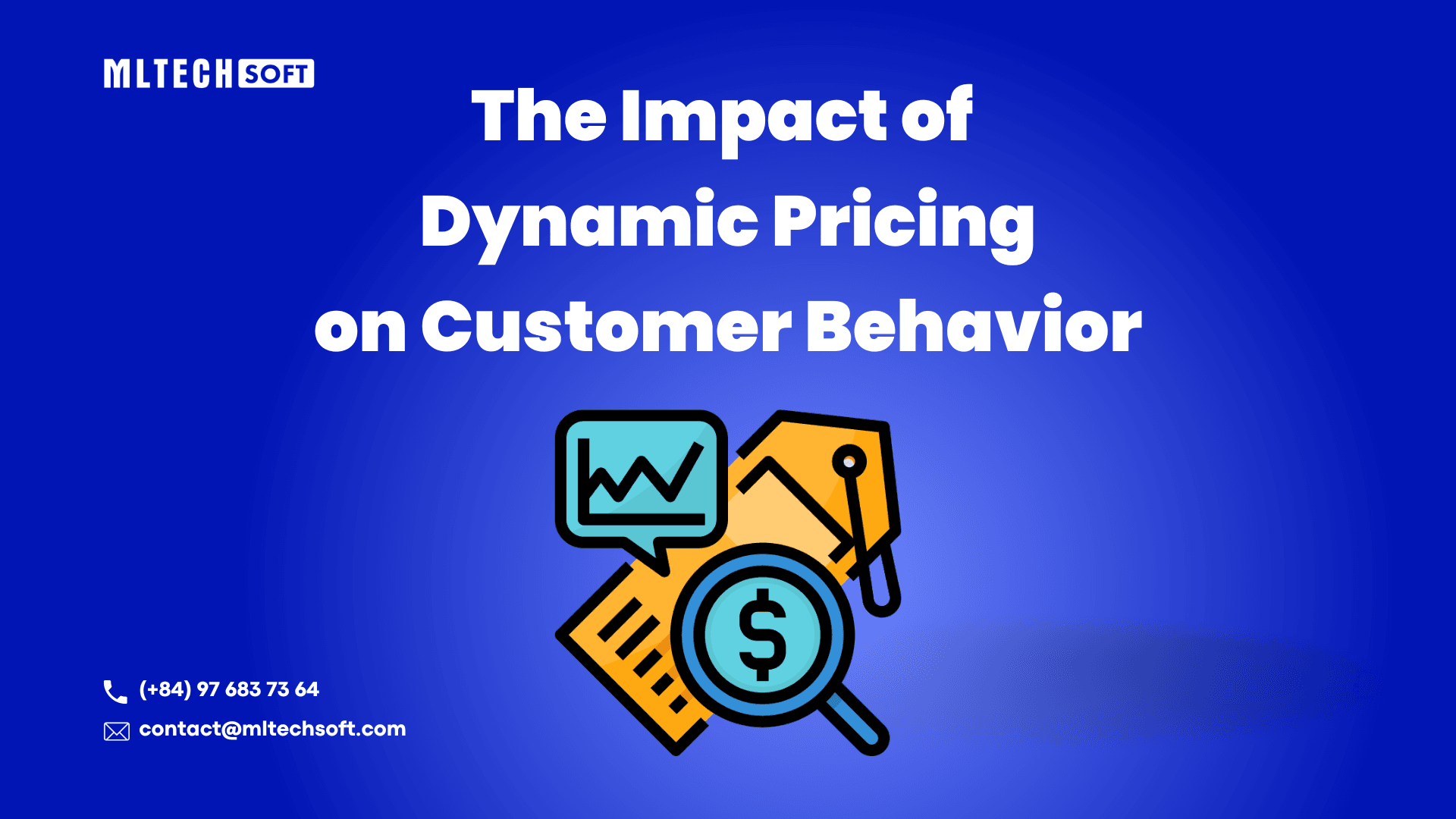
Project Management
The Impact of Dynamic Pricing on Customer BehaviorExplore the impact of dynamic pricing on customer behavior and learn how to implement effective pricing strategies.
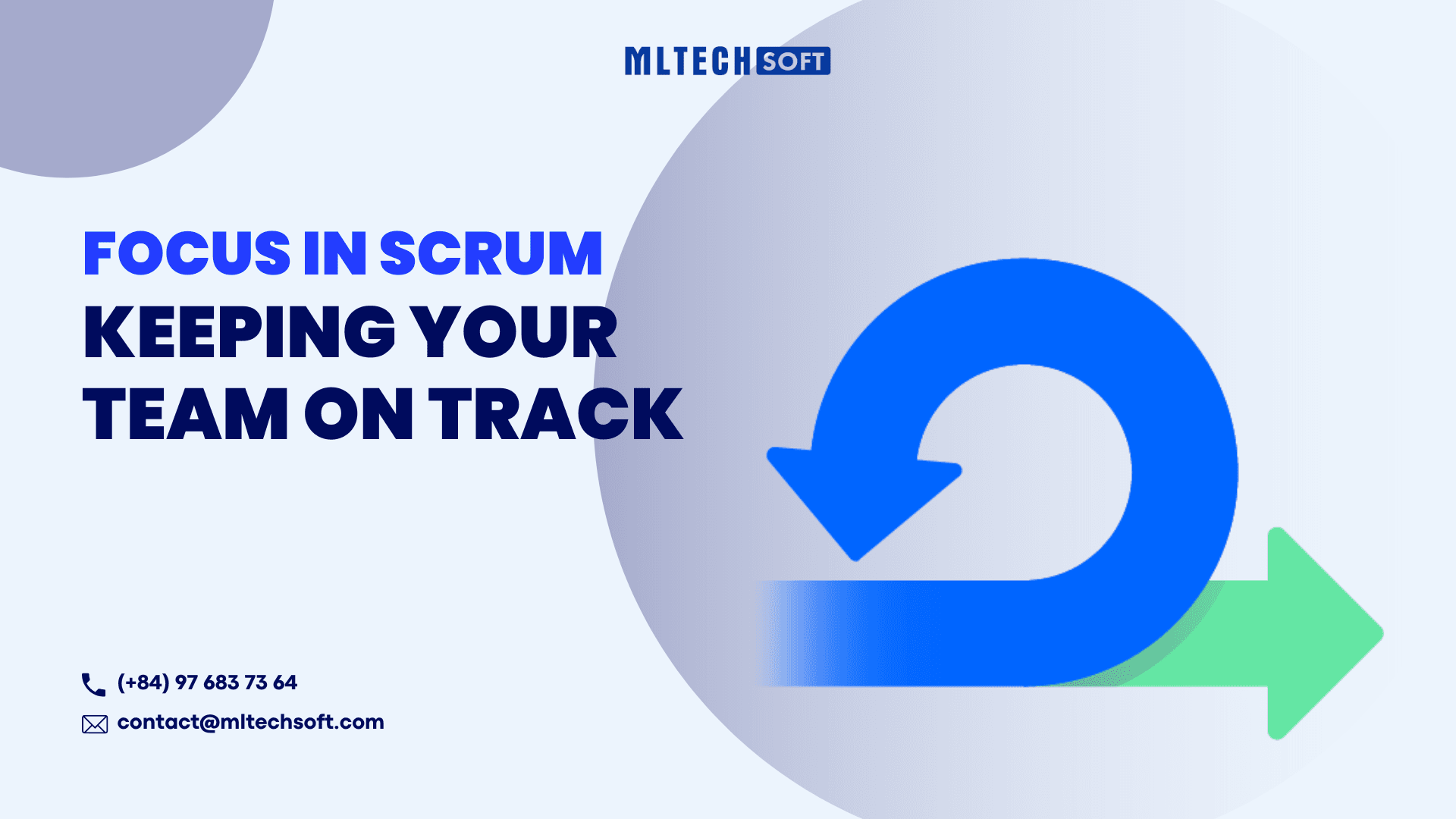
Project Management
Focus in Scrum: Keeping Your Team on TrackDiscover effective strategies to maintain focus within your Scrum team, overcome common challenges, and boost productivity.
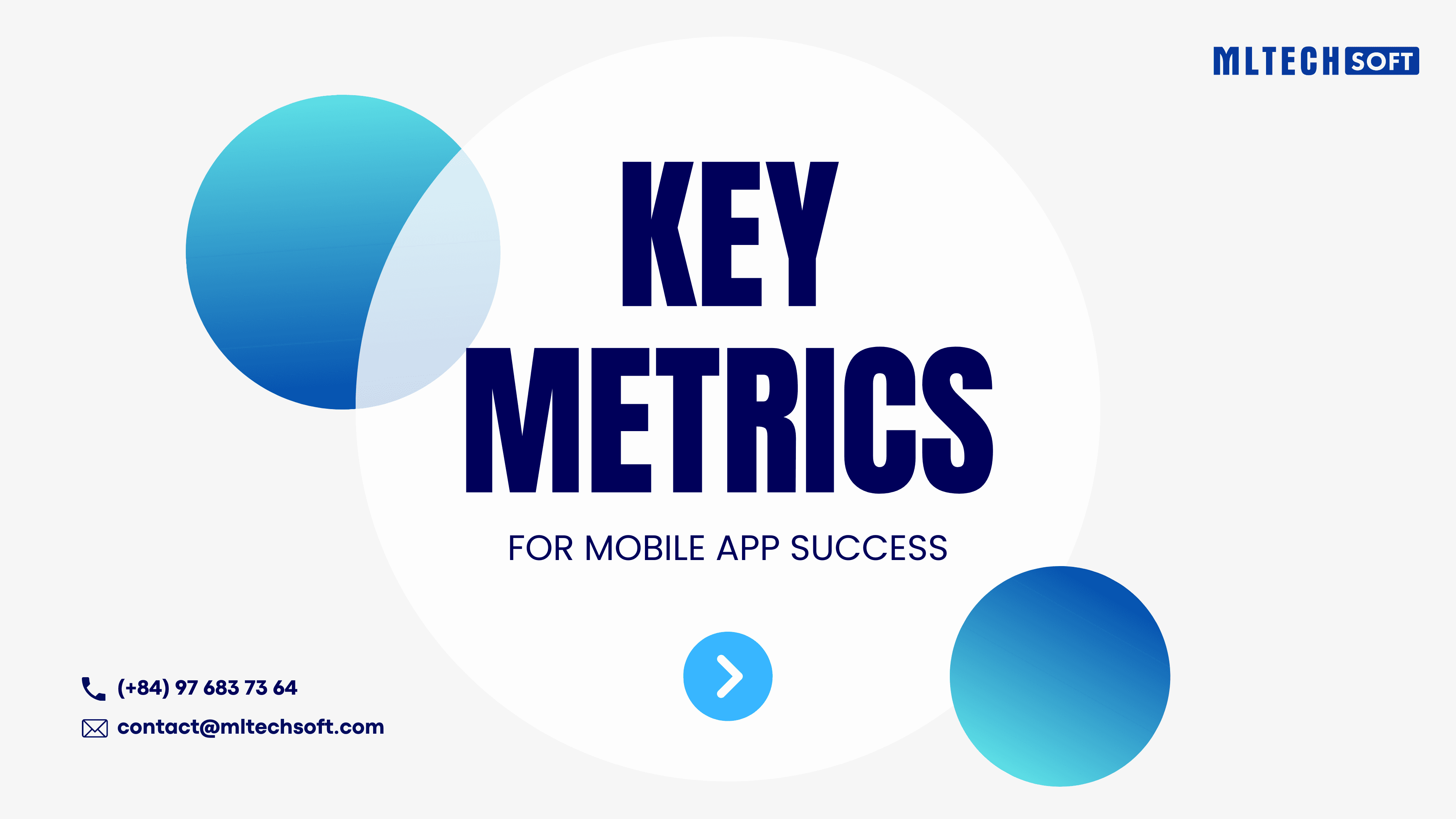
Project Management
Key Metrics for Mobile App SuccessDiscover the essential metrics for mobile app success, from user acquisition and engagement to monetization and performance.
MLTECH SOFT